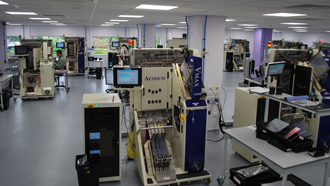
What makes Swindon Silicon stand out is its adherence to producing application specific ICs (ASICS), a product technology which took a battering with the rise of the field programmable device.
Richard Mount (pictured), Director of Sales and Marketing at SSS makes a persuasive case for the ASIC.
“We sit down and talk to customers and you can soon discover they all have individual needs.
“We make a tyre pressure sensor and the fact is that tyres are different from car to car. They all have different requirements.”
“They make a technical case to us,” Mount continues. “They are clear about what they want from the performance of the chip. And we have to be sure we meet their demands.”
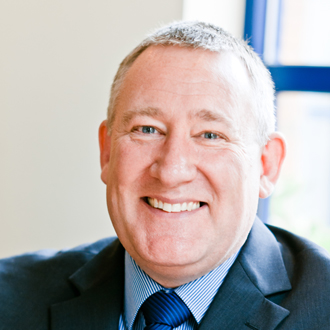
“Producing ASICs is not a necessarily a fast process. It can take nine months to produce samples and it can be up to two years to full production with a device that meets all the automotive industry standards.”
“It’s a big investment by us and the customer,” Mount asserts. “It is a partnership.”
Testimony to Swindon Silicon’s expertise is that it holds 50% plus of the tyre pressure monitoring systems market and it can boast a blue-chip parade of its automotive customers including Jaguar, BMW, Mercedes-Benz, Volvo and Land Rover alongside Peugeot, Citroen and Volkswagen.
The company started business in an office above a dentist, and then to an old schoolhouse via a scout hut, something of a contrast to the modern facility it now occupies on the fringes of Royal Wootton Bassett in Wiltshire.
No disrespect to dentists but it is a better environment for the team of top division design and test engineers housed in the facility. The engineering team boasts 47 engineers, eight boasting PhDs, and 13 with MSc qualifications. And these people brim over with experience – their average directly related work experience totals a tidy 15 years.
What they bring perhaps more than any other attribute is the ability to integrate a host of semiconductor features on a chip.
One question is why ASICs? Richard Mount jumps right in.
“The customer has to ask is an ASIC required?” he explains. “If yes, the benefits are multiple.”
“With our skills we can deliver a product that reduces size, power consumption, weight and most pertinently the cost.”
“And,” adds Mount, “an ASIC provides protection against obsolescence and protects IP.”
The Swindon Silicon team form a close-knit relationship with potential customers from day one.
“The process starts at specification,” says Mount. “Does an ASIC make business sense, is there going to be a return on the investment?”
This initial engagement is designed to flesh out the answers to what the customer wants and what they are trying to achieve. From these first conversations Swindon Silicon develops a product specification and a cost analysis.
Once everybody’s happy to proceed, the Swindon Silicon design team works hand on hand with the customer.
“There’s constant communication through the design process,” says Mount. “Weekly conference calls, and at minimum a monthly face to face sit down.”
There’s little doubt that changes will be made to the initial specification as the design process continues.
“We can handle that,” Mount explains. “In fact we can make changes all the way up to the tape out.”
Swindon Silicon provides a full prototype / engineering sample service by either using MLM (Multi-Layer Mask) or MPW (Multi Project Wafer) engineering wafers. It will provide tested devices at this phase in order to enable the customer to evaluate the device in their system.
Samples are delivered and there can be a conversation about what’s right and what’s wrong.
“The device could be 100 per cent functional but need a tweak,” explains Mount.
Up to 2k devices can be delivered if required. Wafers are held in line at the foundry, usually at metal, during this phase in order to provide flexibility and speed if a design modification is provided and eliminates the requirement of starting new silicon.
Mostly the company uses multi-layer masks which says Mount “are more flexible.”
Says Mount, “We have reduced the test time of Devices Under Test (DUT) but also increased test coverage. This in turn minimises the final device cost but maximises performance through quality. The result is a dramatic increase in product repeatability, yield and overall test quality with a vast decrease in field failure ppm rates.”
Once the ASIC prototype has been evaluated to ensure it is operating to the customer specification, the process then moves into Swindon Silicon’s 3000 square meter test facility. It boasts 50 testers, 40 handlers including six MEMs handlers, and 7 wafer probers that can handle six-inch and eight-inch wafers in a class six clean room.
The team first optimise the design for test (DfT) and manufacturability (DfM) as well as executing the various qualification tests, such as AEC Q100. Optimisation of the wafer probe and ATE test programs are also carried out to ensure high yields and low level ppm figures.
The company undertakes fully automated wafer and package level test, fully automated, online test and QA procedures, 100% wafer level test, 100% package level test. It provides real-time yield statistics, wafer and package level tests correlated, 100% Data log, tri temperature test and burn in.
Swindon Silicon is a fabless company. It partners with companies that offer both wafer packaging and foundry processing.
To meet customer requirements it works with three chip packaging partners covering a variety of options including leadless packages, MEMs packaging and custom packaging.
Chip manufacturing partners again offer an array of manufacturing processes and include global foundry market leader TSMC, alongside ams in Graz, xFAB and TowerJazz.
One other point Mount emphasises is the company’s obsolescence assurance.
“We don’t do obsolescence,” he says.
Security of supply is maintained keeping a store of wafer which can be used as and when needed.
If the manufacturing process is deemed obsolete, then Swindon Silicon will buy wafers to stock until a new design is developed onto a new manufacturing process.
Underlining the point, Mount says, “We still have 30 year old chips out there.”
On exciting project which could bear fruit in 2018 is a partnership with battery management technology specialist Dukosi. The two companies are collaborating to bring Dukosi’s disruptive semiconductor chip based battery management solution to market.
The companies expect that the resulting product will be available in the second half of 2018 supporting multiple end-markets, including the stringent requirements of the global automotive industry.
Dukosi has developed a unique approach to battery management that acquires, processes and stores discrete data directly at the cell. Using novel wireless technology, the system transmits real-time information on cell health and performance to support master level control of the battery pack. This approach optimises system architecture design and management of batteries in electric vehicles, industrial and grid energy storage applications.
In 2015 Swindon Silicon Systems became part of the $3.3bn Sensata Technologies Group, which has two strings to its sensors bow, providing both sensing solutions and performance sensing. It is a major supplier to the automotive market which represents just under two thirds of its business, and the industrial and heavy vehicles, off road (HVOR) markets.
“The acquisition gives us more clout,” agrees Mount, has the potential to open up new markets for us and enables us to do what we are good at focus on supplying top quality solutions for our customers.”