The Future is Silicon, Your Future is Swindon
The Future is Silicon
Constant improvements in silicon design and manufacturing processes are opening the world of Application Specific Integrated Circuits (ASIC) to many more applications and manufacturers. Today’s high quality and high reliability foundry Process Design Kits (PDKs) and models now allow for no risk development with timescales and budgets calculated and agreed prior to project start.
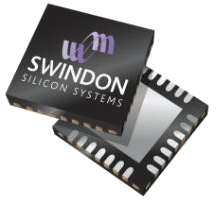
Manufacturing Technology Megatrends and ASIC Solutions
A whole new generation of manufacturers are turning to silicon and you should be one of them. Many of these new generation manufacturers are behind a variety of new, high volume applications which are being described by many as Megatrends and are driven by the market drivers of electrification, autonomy, smart and connected and clean and efficient.
Examples include the Smart Factory and the Industrial Internet of Things (IIoT), electric and hybrid vehicles, autonomous driving and all manner of applications that require sensor interfaces. These are all applications where silicon will play a major part in a product by adding functionality in a smaller footprint and at ever decreasing costs.
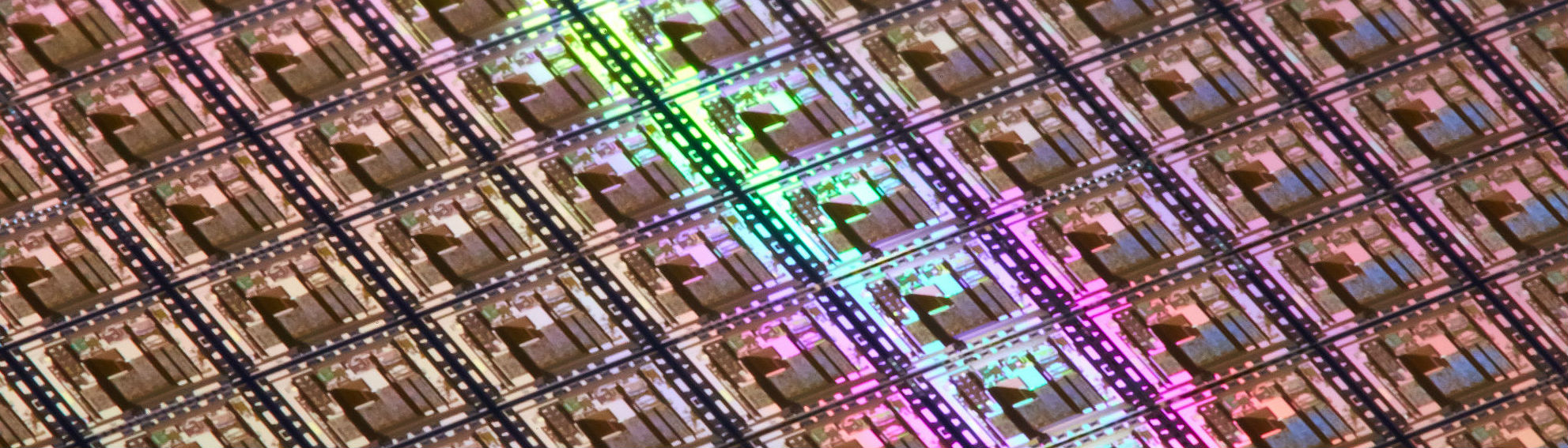
Six Key Reasons to use an ASIC Silicon Solution
Here are the key reasons why you should consider an ASIC silicon solution for your next generation product – beginning with functionality and continuing with design and manufacturing costs, timescales as well as other less obvious benefits.
1. Unique Functionality
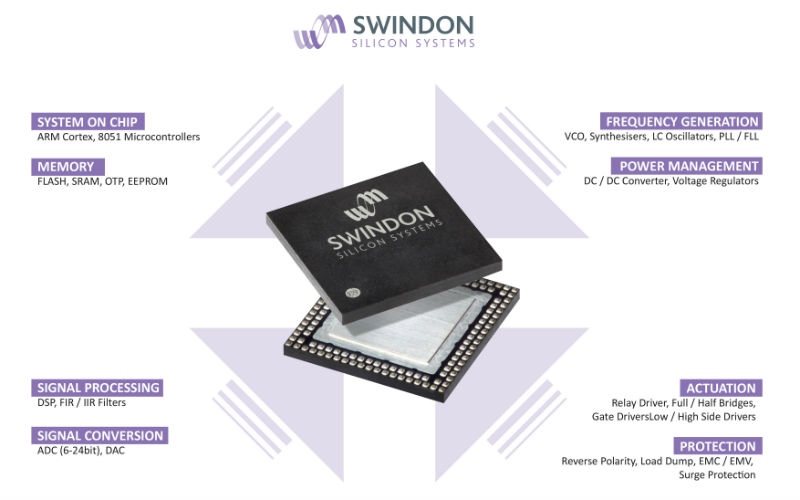
All this adds up to a silicon device that is functionally unique to you and exactly meets the requirements of your application.
2. Design Cost
The ever-increasing availability of foundry and third-party IP has changed the way integrated circuits are designed – from handcrafting every function at the transistor level to using existing IP blocks that have been verified in a known environment.
Over a relatively short number of years the cost of designing custom silicon has fallen dramatically and the long-held myths of projects over-running budget are long gone.
Experienced ASIC companies have significant existing silicon-proven IP libraries that they can leverage along with other commercially available IP, which assists greatly in keeping design times down and costs to a minimum.
With a focus on versatile and proven engineering solutions, some ASIC companies can deliver a turnkey experience that’s often more affordable than you would expect.
3. Cost of Manufacture
Many of today’s applications are generally based on mixed signal designs using geometries from 55nm up to 350nm. As the high-volume consumer electronics market is primarily served by digital designs and ever reducing geometries, there is an availability of the geometry nodes that fit the mixed signal design. These geometries may not be suitable for the very latest, highly integrated, and high-performance digital ICs, but they remain ideal for mixed-signal solutions both technically and from a cost perspective.
To maximize their foundry utilisation, manufacturers need to continually attract new customers. They achieve this by offering competitive engineering costs both in wafer production and production tooling such as masks and IP.
These low manufacturing costs can be improved still further when partnering with an established full turnkey ASIC company like Swindon. This is achieved by the economies of scale that an established ASIC company has by leveraging its current wafer portfolio on future wafer purchases. This will allow new customers to “punch above their weight”. Partnering with an established ASIC full turnkey suppler means it’s more affordable than ever to create custom silicon.
4. Timescale
Time to market is one of the most important aspects of any new product development and it is here that huge strides have been made over the last decade or so. A custom ASIC no longer means a hand-crafted design mainly thanks to the availability of IP, as already discussed, and this can greatly reduce the development time for your device. Additionally the process flow and engineering sample availability that the silicon foundries now offer is much more flexible and allows for time saving over traditional approaches like the Multi Project Wafer (MPW) route.
It is important to note that very few ASICs are designed from a blank drawing board. At the very least, established ASIC designers will have the relevant IP library to form a foundation for the chip in question. But the most important aspect in terms of timescales is the skill and experience of the team of designers working on the ASIC.
Design for test, robustness in production and the inevitable qualification criteria such as the automotive AEC Q100 is fundamental to take into consideration in the design phase. Stray from this proven methodology and timescales can be stretched. A turnkey ASIC company takes all this into consideration at the planning stages to ensure a timely design and production schedule ending in a fully qualified ASIC of the highest quality.
5. IP Protection
One of the principal reasons why a company will commission an ASIC is to protect its Intellectual Property (IP). The strength of an ASIC is that it is extremely difficult to re-engineer the IC or for it to be “re-used” in other designs. Here at Swindon we provide our customers full ownership of the completed system design ensuring that the IP of the final solution remains firmly in the customer’s possession.
6. Non-Obsolescence
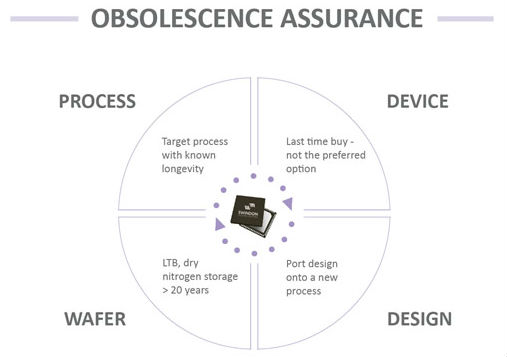
Obsolescence is the bane of every purchasing department but it is a potential issue that can be solved by the ASIC.
Your Future is Swindon
We are a leader in high performance and low-cost mixed signal ASICs. We are part of Sensata Technologies, one of the World’s leading suppliers of sensing, electrical protection, control and power management solutions, and have no less than five decades experience in the design, production test and supply of ASICs for applications in automotive and across many industrial sectors.
Experts in Mixed Signal Integration
There are many IC companies who can only claim expertise in either digital or analog design. However, many of today’s applications require much more than this either/or simplistic approach. The solution is provided by the utilisation of mixed-signal integration which involves working in both domains on a single die and dealing with the issues that will inevitably arise through this added level of complexity.
For example, design engineers need to understand the effects that high-frequency digital can have on sensitive analog circuitry and how the portioning of the die can affect performance between the domains. Working with an ASIC company like Swindon that specialises in mixed signal is crucial as they understand and are experienced in the unique engineering challenges that are involved when designing complex mixed signal circuitry in small geometries. Experienced mixed signal ASIC companies such as Swindon will advise on system performance and engineer an optimised solution while the customer focuses on their aspects of the system performance.
Dealing with these design and layout challenges, while trying to remain within the area and cost budgets, is where an expert in mixed signal ASIC design excels. This requires an extensive electronics and physics understanding and the experience to implement techniques that provide known solutions, whether that involves a full-custom design or using existing IP that is known to work in the required system application.
Global Leader in ASIC Solutions
Swindon is the global leader and foremost supplier of ASIC/MEMS solutions for Tyre Pressure Monitoring Systems (TPMS), supplying approximately half of the Worldwide demand. We bring this global leadership to everything that we do.
EV battery management is another significant automotive application for Swindon. The rise of the hybrid and electric vehicle has brought the need to monitor individual cells in the multicell battery power pack and constantly communicate each cell’s State of Charge (SOC) and State of Health (SOH) status to the vehicle’s engine management system. This new generation automotive fuel gauge is another area where the ASIC solution is providing performance, cost and reliability advances whilst ensuring that stringent functional safety criteria (ISO 26262) are incorporated at chip level.
Design Team Partnership
ASICs are complex devices containing many functions – checkout our IC Builder link for an indication of what can be included. So, not surprisingly, choosing a supplier that understands your application’s technical, commercial, qualification and functional safety requirements, from the outset, is hugely important.
All successful ASIC-based projects rely on the close intellectual co-operation between the customer’s designers and the chip supplier’s design teams.
An initial contact will satisfy the customer that its application does, or does not, suit the ASIC route and that the chip supplier understands the requirement and has the expertise and capacity to complete the project. At this initial meeting, both customer and supplier need to be satisfied that the project has a future.
Once the partnership begins, there is very close co-operation between both teams. A Technical Lead and a Project manager will be assigned for the duration of the project and liaise on all aspects of the project with the customer’s counterparts. This close relationship we believe is crucial in the ongoing success of the design and project and the future production.
Complete ASIC Full Turnkey Package
Swindon provides what is called a full turn key (FTK) solution which commences with the ASIC specification, design, simulation, layout and verification and continues with the evaluation, qualification and in-house production test (both wafer probe and packaged devices) of the ASIC. This also includes wafer fabrication, packaging and evaluation of engineering samples, pre-production and production devices.
Our supply chain management team works with our customer’s purchasing teams to ensure on time delivery of 100% production tested devices to a place of the customers choosing and to ensure this, we have production test facilities in both Europe and Asia. The FTK service is concluded with the ongoing Quality Assurance team that audits and monitors the foundry and packaging houses.
The advantages of this FTK service provision are many ranging from one point of contact for project and / or production issues to the warranty of the production device being with Swindon.
Our customers gain access to leading in-house design and production test and calibration facilities. We provide customers with a competitive advantage, both technical and commercial, and guarantee the supply of the highest quality ASICs for the lifetime of their product.
Supply Guaranteed
We achieve this with careful selection of the fabrication processes we select for use in a specific project based upon technical and commercial requirements. Once the device is in volume production, the Swindon team ensures that there are finished goods in stock to satisfy immediate requirement and the there is sufficient Work in Progress (WiP) in line to satisfy future demand. On time every time.
Your Next Step
It is an easy process to establish the approach we take when discussing your project. Your design team will have a clear idea about the product you are developing, the timescales involved and the budget. All aspects of the process flow, development and payment milestones are agreed prior to commencing the project and there are no hidden costs. Swindon will quickly show you how its engineering excellence in delivering the latest ASIC technology will help to differentiate your product from your completion and ensure a commercial and technical advantage.